2. Remove the #1 main bearing cap. Remove the old bearings and clean the connecting rod and cap cradles with a clean, lint-free cloth. They must be perfectly clean!
Checking the operating clearance of connecting rod bearings
3. Clean the new top bearing from the back and install it in the connecting rod. Then install the other insert from the kit into the cover. Make sure that the lug of the bushing fits into the notch of the connecting rod or cap (see fig. 18.3).
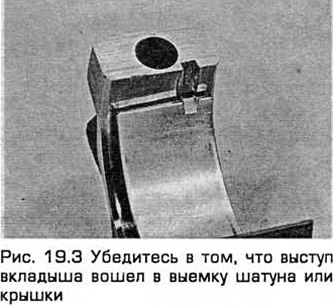
Caution: Do not hammer bushings into place and do not scratch bearing surfaces. Do not apply lubricant at this stage.
4. When installing, the mating surfaces of the bearing components must be perfectly clean and free of grease.
5. Position the piston ring gaps as indicated in paragraph 16. Lubricate the piston and rings with clean engine oil and install a piston ring compressor on the piston. Compress the rings so that they are flush with the piston.
6. Rotate the crankshaft so that the #1 cylinder journal is at bottom dead center and lubricate the cylinder with clean engine oil.
7. Install the connecting rod and piston group of cylinder No. 1 so that the arrow on the piston bottom points towards the toothed belt. The numbers corresponding to the cylinder number, etched on the machined surface of the connecting rod and its cover, must be visible from the front (from the engine outlet) (see fig. 9.5,a and 9.5.6). Carefully insert the connecting rod and piston group into cylinder #1 and support the bottom edge of the piston ring compressor on the cylinder block.
8. Tap the top edge of the ring compressor to make sure it rests on the block all the way around.
9. Tap the piston head lightly with a wooden mallet (see fig. 19.9). resting the connecting rod on the connecting rod neck. Press down on the compressor with a little force so that the piston rings do not pop out of it before entering the cylinder. Proceed slowly and if you feel resistance as the piston enters the cylinder, stop immediately. Find the cause of the jam and fix it. Never force the piston into the cylinder to avoid breaking the ring and/or piston.
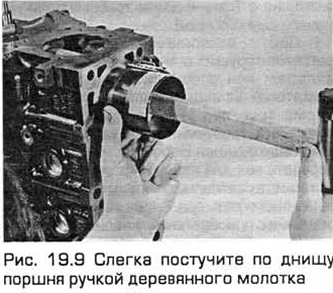
10. To control the operating clearance of the connecting rod bearings, cut a piece of plastic thread from a set of the appropriate size. It should be slightly shorter than the width of the connecting rod bearing. Lay a piece of thread on the connecting rod journal of cylinder No. 1 parallel to the axis of the crankshaft (see fig. 17.6).
11. Clear mating surfaces of a rod and a cover and establish a cover of a rod bearing. Make sure. that the number etched on the cap is on the same side as the connecting rod (see fig. 19.11). Tighten the cover bolts evenly - first with a torque wrench, to the required torque, and then with a head and a wrench, as well as a protractor, to a regulated angle. Use a thin-walled head to prevent it from getting stuck between the cap and nut. If the head still jams, then slightly raise it so that it does not touch the cover. Do not rotate the crankshaft while performing this operation!
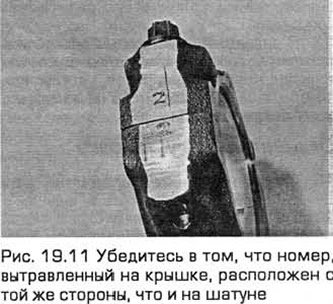
12. Without moving the thread, unscrew the bolts and remove the cover.
13. Determine the crushed thread width from the template to obtain the working clearance. Compare it with the technical requirements.
14. If the gap does not correspond to the regulated, consult with dealers. If at the same time the crankshaft journals are normal, then, perhaps, in order to achieve a regulated clearance, it is only necessary to replace the liners. If this is not possible, then the crankshaft must be reground by specialists who can also sell you liners of the required repair size. Immediately after measuring the working clearance, you need to check that no dirt or oil has got between the liners and the connecting rod or cover. It is also necessary to re-check the diameter of the connecting rod journal. If the thread is wider on one side than the other, then the crankpin may have a taper.
15. Carefully remove the remaining thread from the neck and the working surface of the bearing. Do not scratch the bearing, but work with a fingernail or a piece of non-rigid plastic.
Final installation of the connecting rod and piston group
16. Make sure the bearing surfaces are perfectly clean, then lubricate them with an even coat of clean molybdenum disulphide grease or clean engine oil. Push the piston into the cylinder.
17. Install the connecting rod on the crankpin, install the connecting rod bearing cap and tighten the bolts in two stages (see above).
18. Repeat the entire procedure for the rest of the connecting rod and piston groups.
19. In doing so, it is important to consider the following:
- A) The back side of each bushing and the lodgement of the connecting rod and cap must be perfectly clean during assembly.
- b) Make sure. that you insert the connecting rod and piston group into its corresponding cylinder (according to the marking on the front side of the connecting rod and its cover).
- V) The arrow on the piston crown must point towards the toothed belt (4 cylinder engines) or timing chains (see fig. 19.19).
- G) Lubricate the cylinders with clean engine oil.
- d) When installing connecting rod caps (after completion of the working clearance check) lubricate the running surfaces of the bearings.
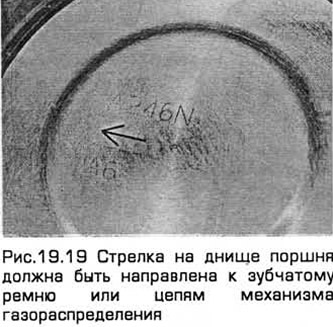
20. After installing all the connecting rod and piston groups, turn the crankshaft by hand a few turns to check for seizing.
21. On 4-cylinder engines manufactured from 05.1998, apply sealant to the joints between the cylinder block and the oil pump / cuff housing. Then install a new gasket separating the cylinder block and lower crankcase. Install the lower crankcase on the cylinder block, insert the bolts and tighten them by hand. Place a straight edge on the surfaces of the cylinder block and lower crankcase mating with the transmission to check the alignment of the cylinder block and lower crankcase. The lower crankcase must be flush with the cylinder block. If this is not the case, then:
- A) On non-automatic transmission models, adjust between a position where there is a gap of 0.25 mm between these surfaces and a position where they overlap by 0.1 mm.
- b) On models with automatic transmission, adjust between a position where there is a gap of 0.25 mm between these surfaces and a position where they are flush.
Visitor comments