The basic principle of ignition is that the battery current flows through the primary winding of the ignition coil, made of several turns (about 100) thick copper wire. The impact of an electric current creates a strong magnetic field around the iron core in the ignition coil, i.e. current energy is converted into magnetic field energy.
As the piston approaches TDC on the compression stroke, when the fuel mixture is to be ignited, electrical current is interrupted to the ignition coil.
When the electric current is interrupted, the magnetic field disappears, inducing in the secondary winding of the ignition coil, made of a large number of turns of thin wire (section approx. 0.1 mm2), high voltage current.

TECHNICAL DICTIONARY
Sensors
Pressure meter.
Connected by a hose to the suction pipe, it transmits information to the control unit about the vacuum in the suction pipe. The sensor is made in the form of a pressure-sensitive crystal chip. By changing its electrical resistance, it reacts to the rarefaction at the moment. From these indicators, as well as information about the speed of the crankshaft at the moment, the control unit determines the current operating state of the engine.
Knock sensor.
The process of fuel combustion in the engine cylinders is controlled by the engine control unit based on information received from the knock sensor. Knocking combustion of fuel occurs when the ignition is too early and the engine is running on fuel with a low octane rating. Knocking occurs when the speed of flame propagation in the combustion chamber approaches the speed of sound, mainly towards the end of the combustion process, and the residual gases are sufficiently compressed and have a high temperature. Detonation is characterized by very high impulse pressure, which leads to overheating of the engine, damage to the piston, cylinder head and crankshaft bearing shells.
The knock sensor reacts to the high-frequency vibrations of the cylinder block that occur during detonation and transforms them into electrical signals that enter the control unit. This information is then compared with the signals obtained during the combustion of the fuel without detonation. When knocking occurs, the ignition timing is shifted to the side of delay until the combustion process occurs normally.
Crankshaft speed sensor.
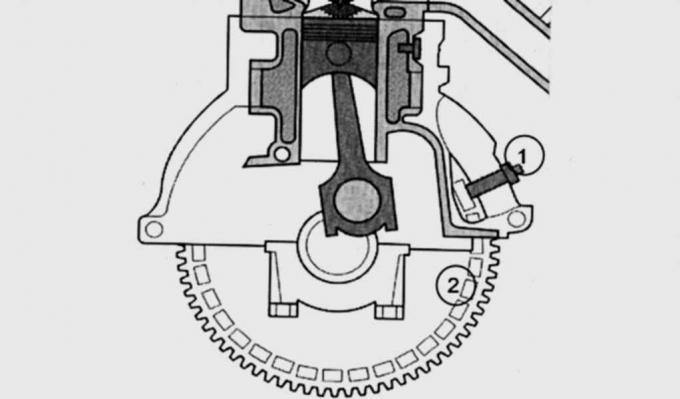
Pic. 9.2. The location of the inductive pulse sensor that transmits information to the control unit about the speed and position of the crankshaft: 1 - inductive sensor; 2 - rotor plates
An inductive sensor has a wire winding coil and a magnet. A rotor is used as a mating part, consisting of plates of a certain size (pic. 9.2). Each time the rotor plate passes near the impulse sensor, the magnetic field changes, as a result of which an impulse voltage is induced in the coil winding. Based on the number of pulses, the control unit calculates the engine speed.
To calculate the ignition timing, the control unit needs information about the position of the crankshaft. To do this, the rotor for cylinders 1 and 4 has two longer plates in front of the top dead center of each cylinder. When passing through the section of the rotor with elongated plates, it does not induce voltage for a short moment. Based on the short-term absence of voltage pulses, the control unit determines the position of the engine crankshaft for cylinders 1 and 4.
This high voltage current of the ignition system is directly applied to the spark plug, between the electrodes of which a spark discharge is formed. The fuel mixture ignites and presses on the piston, which turns the engine crankshaft through the connecting rod. The electrical circuit is switched on again and the cycle repeats.
Models from the 96 series are equipped with an electronic ignition system with two ignition coils. With each control pulse of current supplied by the control unit, the ignition coil sends a pulse to two spark plugs at once. One spark ignites the fuel mixture at the end of the compression stroke, and the second occurs on the exhaust stroke, where the ignition spark has no effect on engine operation and is therefore wasted. After a further turn of the crankshaft, the ignition coil again supplies an ignition pulse to two candles at once, but this time, where the spark discharge previously occurred in the cylinder on the exhaust stroke, the compression stroke ends and the fuel mixture ignites, and vice versa. Ignition pulses provide the following sequence of cylinders 1-3-4-2 (Endura-E: 1–2–4–3).
spark source.
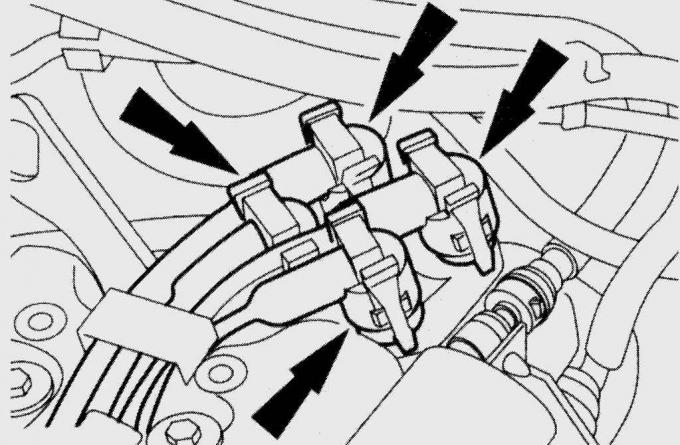
Pic. 9.3. Location of fasteners for high-voltage wire connectors
The electronic ignition unit has little in common with a conventional ignition coil. Sensors, transistors and diodes distribute the ignition sparks to individual cylinders in the control unit. In Zetec-SE engines, the ignition coil is located under the engine upholstery. to disconnect the high-voltage ignition wire, it is necessary to squeeze the tabs of the clamps on the electrical connectors (pic. 9.3).
Visitor comments